As defined by the U.S. Department of State, there are currently 59 foreign terrorist organizations listed on the agency’s site. Designated as such beginning in late 1997 through August of 2014, these terrorist organizations present a dire threat to the United States and her Allies.
To counter such perils, today’s warfighter must have the latest communication technologies at hand to know when, where and how to destroy threats and to counter terrorist and enemy state activities. This information has to be immediate, mobile, viable and interception adverse.
A step forward in this crucial direction for the United States is the recent launch of the U.S. Navy’s MUOS-3 satellite, built by Lockheed Martin and launched by United Launch Alliance.
Operating within the Ultra High Frequency Band, the recently launched third MUOS (Mobile User Objective System) secure communications satellite traveling into geosynchronous orbit offers higher data rates, much improved operational capabilities as well as greater mobility to the MILSATCOM community.
With the ability to connect with legacy terminals and newer, smaller terminals, full operational capability will be attained in 2015 for members of the armed services. This is thanks to the satellite’s vantage point in geostationary orbit, enabling the satellite to cover approximately a third of the Earth’s surface and to use the 14-meter diameter reflecting mesh antenna to communicate with ground-based users.
As stated by Iris Bombelyn, V. P. of Narrowband Communications at Lockheed Martin, “The addition of this satellite will give the MUOS constellation coverage over more than three-quarters of the globe, further extending the reach of the advanced communications capabilities MUOS will provide our mobile warfighters.”
MUOS-3 will eventually replace the legacy system already on orbit, with MUOS-1 and MUOS-2 having been in operation since February of 2012 and July of 2013, respectively.
Looking forward, MUOS-4, in December of last year, completed thermal vacuum testing at Lockheed Martin’s Dual Entry Large Thermal Altitude chamber, directly following the shipment of MUOS-3 to the Cape Canaveral Air Force Station for launch. The next step for MUOS-4 is the final integrated system testing. Later this year, expect the launch of MUOS-4, with MUOS-5 scheduled for a 2016 launch. There are a total of five MUOS spacecraft contracts for the company.
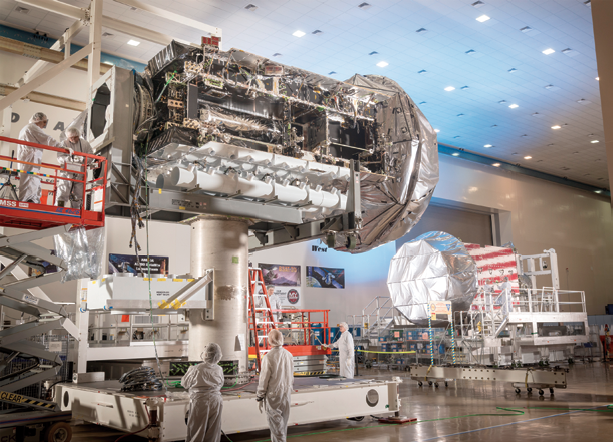
MUOS-3 during the satellite’s build process. Photo is courtesy of Lockheed Martin.
A United Launch Alliance Atlas V Evolved Expendable Launch Vehicle (EELV) 551 configured rocket boosted the MUOS-3 into orbit on January 20, 2015 to an altitude of 22,000 miles above the Earth. The launch occurred from Space Complex 41.
The EELV program was established by the United States Air Force to provide assured access to space for Department of Defense and other government payloads. The commercially developed EELV program supports the full range of government mission requirements, while delivering on schedule and providing significant cost savings over the heritage launch systems.
The United Launch Alliance MUOS-3 Mission Booklet reveals that the satellite was encapsulated in a 5 meter (14-ft) diameter medium payload fairing (PLF), which is a sandwich composite structure made with a vented aluminum-honeycomb core and graphite-epoxy face sheets. The bisector (two-piece shell) PLF encapsulates the Centaur second stage and the satellite itself. The vehicle’s height with the PLF is approximately 206 ft.
The Centaur second stage is 10 ft in diameter and 41.5 ft in length with propellant tanks constructed of pressure-stabilized, corrosion resistant stainless steel. Centaur is a cryogenic vehicle, fueled with liquid hydrogen and liquid oxygen and uses a single RL10C-1 engine producing 22,900 lbs of thrust.
The cryogenic tanks are insulated with a combination of helium-purged insulation blankets, radiation shields, and spray-on foam insulation (SOFI). The Centaur forward adapter (CFA) provides the structural mountings for the fault-tolerant avionics system and the structural and electrical interfaces with the spacecraft.
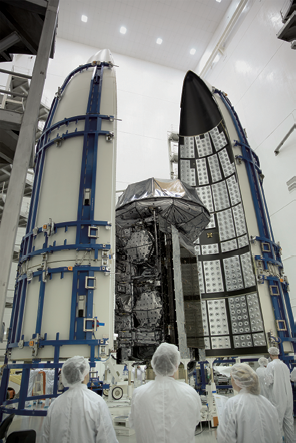
MUSO-3 encapsulation within the fairing. Photo is courtesy of Lockheed Martin.
The Atlas V booster is 12.5 ft in diameter and 106.5 ft in length. The booster’s tanks are structurally rigid and constructed of isogrid aluminum barrels, spun-formed aluminum domes, and intertank skirts. Atlas booster propulsion is provided by the RD-180 engine system (a single engine with two thrust chambers). The RD-180 burns RP-1 (Rocket Propellant-1 or highly purified kerosene) and liquid oxygen, and delivers 860,200 lbs. of thrust at sea level.
Five solid rocket boosters (SRB) generate the additional power required at liftoff, with each SRB providing 348,500 lbs. of thrust. The Atlas V booster is controlled by the Centaur avionics system, which provides guidance, flight control, and vehicle sequencing functions during the booster and Centaur phases of flight.
Jim Sponnick, United Launch Alliance Vice President of the Atlas and Delta Programs said, “The MUOS-3 satellite is the heaviest payload to ride into space atop any of ULA’s Atlas V launch vehicles. The Atlas V will generate more than two and a half million pounds of thrust at liftoff in order to meet the demands of lifting the nearly 7.5-ton satellite. The ULA team is focused on attaining Perfect Product Delivery for the MUOS-3 mission, which includes a relentless focus on mission success (the perfect product) and also excellence and continuous improvement in meeting all of the needs of our customers (the perfect delivery).”
Participating in the launch with their crucial role was Aerojet-Rocketdyne, as ULA’s Atlas V rocket used five AJ60 solid rocket boosters (SRB), an RL10C-1 upper-stage engine and several spacecraft attitude control thrusters. The AJ-60A was developed from 1999 to 2003 as a commercial low cost strap-on booster for the Atlas V launch vehicle.
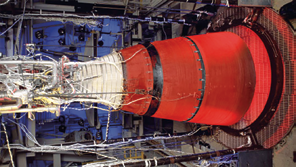
The AJ60 rocket engine. Photo is courtesy of Aeroject-Rocketdyne.
The motor is configured with a thrust profile that reduces aerodynamic loads during max-Q and thrust-differential during tail-off. It can be configured for other applications that require a different case length and/or attach interface requirement. It could also be used as an in-line stage for small launch vehicles or strategic missiles.
The composite graphite fiber and Aramid-filled EPDM insulation monolithic motor case has no segmented joints, thus eliminating historical failure modes and provides functional and operational simplicity. At 62-inches in diameter and 669-inches in length, this is the largest monolithic motor currently in production in the world.
The motor nozzle is fixed at a 3-degree cant; however, the nozzle can be upgraded with a flexseal TVC for steering. Both the throat and exit cone are fabricated with carbon-phenolic composite materials.
The five AJ60 SRBs were ignited at lift off, increasing the launch thrust of the Atlas V rocket by more than 1.9 million pounds. All Atlas V launches requiring extra boost performance have flown Aerojet Rocketdyne-produced SRBs. These motors have demonstrated a 100 percent success record in flight since the first Atlas V launch with SRBs on July 17, 2003.

Artistic rendition of the MUOS-3 satellite. Image courtesy of Lockheed Martin.
A single RL10C-1 engine delivers 22,890 pounds of thrust to power the Atlas V upper-stage, burning cryogenic liquid hydrogen and liquid oxygen propellants. Created in 1959, after Aerojet-Rocketdyne engineers harnessed high-energy liquid hydrogen as fuel for aerospace propulsion, the RL10 has helped place numerous military, government, and commercial satellites into orbit, and has powered space-probe missions to nearly every planet in our solar system.
Some of the engine’s notable interplanetary missions include the Surveyor Lunar Lander, Viking Mars Lander and the Voyager Outer Planets Fly-By; while its heritage includes supporting MILSTAR, EUTELSAT, TDRS ECHOSTAR, INTELSAT, GALAXY, DSCSIII, and JCSAT satellites.
The RL10 continues its legacy as the industry workhorse, with two separate models supporting the latest versions of United Launch Alliance’s (ULA) launch vehicles. The RL10A-4-2 powers the upper stage of the Atlas V, and the RL10B-2 powers the upper stage of the Delta IV. The RL10B-2 also features the world’s largest carbon-carbon extendable nozzle. This high-expansion ratio nozzle enables the RL10B-2 to achieve 465.5 seconds of specific impulse and lift payloads of up to 30,000 lbs.
In addition to the five SRBs and upper-stage engine, 12 Aerojet Rocketdyne monopropellant (hydrazine) thrusters in four modules on the Atlas V Centaur upper stage provided roll, pitch and yaw control as well as settling burns for the upper stage main engine. ARDÉ, a subsidiary of Aerojet Rocketdyne based in New Jersey, provides the pressure vessels on the first and second stages on the launch vehicle.
Additional launch support was provided by ATK. The company delivered critical hardware for MUOS-3 and the United Launch Alliance (ULA) Atlas V launch vehicle. Using advanced fiber placement manufacturing and automated inspection techniques, ATK produced three components for the ULA Atlas V vehicle, including the 10-foot diameter composite heat shield that provides essential protection to the first stage engine, the Centaur Interstage Adapter (CISA) that houses the second stage engine, and the boattail that adapts from the core vehicle to the five-meter diameter fairing. The structures were fabricated by ATK at its Iuka, Mississippi, facility. This is the 52nd Atlas V launch using ATK-built composite structures.
The Atlas V rocket flew in the 551 vehicle configuration with a five-meter fairing, five solid rocket boosters and a single-engine Centaur upper stage. ATK manufactured the Reaction Control System propellant tank for the Atlas V at its Commerce, California facility.
This flight marked the 17th successful flight of the ATK retro motors. Eight of these solid motors supported separation of the spent first stage. The Atlas retrorocket is built at ATK’s Elkton, Maryland, facility.
For the MUOS-3 satellite, ATK provided multiple components and structures from the following company locations: San Diego, Goleta, and Commerce, California; Magna, Utah; and Beltsville, Maryland.
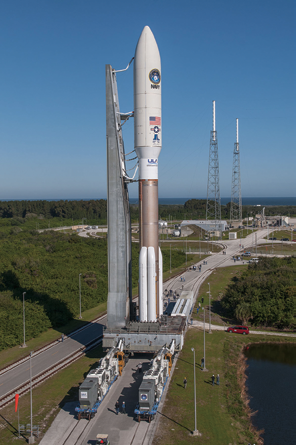
Atlas V with MUOS-3 payload enroute to the launch pad. Photo is courtesy of United Launch Alliance.
Additionally involved with this launch of the Atlas V rocket, built by ULA, was engineering analysis and simulation software from Siemens’ product lifecycle management (PLM) software business. Siemens PLM software is used throughout the global space industry to help increase efficiency, reduce costs and ensure mission success.
No less than 18 of the top 20 Original Equipment Manufacturers (OEMs) in the aerospace and defense sectors use Siemens PLM software solutions for constructing, designing and simulating rockets, satellites and space shuttles. NASA’s Mars rover Curiosity, which was made for the 2012 mission to Mars, is the best example of this successful cooperation.
High Definition Product Lifecycle Management (HD-PLM) solutions are based on three core principles:
• Intelligently integrating information to extract value from large volumes of a wide variety of data, providing users meaningful assistance in decision-making
• Future-proofing the PLM architecture to preserve client investment in the solutions, minimize the total cost of ownership and enabling the ability to take advantage of change
• Providing a “high-definition” user experience so that everyone involved in making your products gets the information they need in a form that’s best suited to their job, in the simplest and fastest way possible
By providing intelligently integrated information at exactly the right time, in the correct context, and with the precise level of detail for everyone involved in your product lifecycle process, HD-PLM helps to achieve a new level of productivity, make smart timely decisions, and deliver great products. That’s the vision of HD-PLM—and that’s the goal of Siemens PLM Software.
A Siemens HD-PLM Vision white paper PDF is downloadable at
https://www.plm.automation.siemens.com/en_us/about_us/facts_philosophy/index.shtml#lightview%26uri=tcm:1023-155767%26title=HD-PLM%20Vision%20-%20Siemens%20White%20Paper%20-%2026286%26docType=.pdf.
The prime contractor and system integrator for MUSO-3 is Lockheed Martin. The MUOS program responsibility rests with the Navy’s Program Executive Office for Space Systems and their division’s Communications Satellite Program Office that’s based in San Diego, California.
The Mobile User Objective System provides netcentric use of UHF SATCOM, as well as the following enabling capabilities:
• Beyond line-of-site communication for mobile warfighters with focus on usability
• Global communications to connect any set of users, regardless of location with the exception of polar regions
• Improved connectivity in stressed environments including urban canyons, mountains, jungle, weather and scintillation
“Bandwidth on Demand” architecture that is future upgradeable with “smarts” on the ground and accessibility to Global Information Grid (GIG), Non-secure Internet Protocol Router Network (NIPRNet), Secure Internet Protocol Router Network (SIPRNet), and Defense Information Systems Network (DISN)
On-orbit testing was initiated directly after the satellite’s solar arrays and antennas were deployed, with turn-over to the U.S. Navy for additional testing and service commissioning. Once such has occurred, the premium result will be 16x the capacity of the legacy systems, thanks to waveform that enables priority capacity assignments and Wideband Code Division Multiple Access (WCDMA) technology.
MUOS is similar in operation to a smartphone cell tower high in the sky. With BLOS (Beyond-Line-Of-Sight) capabilities, comms will occur between the satellite and warfighters via an Internet-like, protocol-based system and leverages 3G mobile communications technology.
With improved ground communications for U.S. Forces, the ability to use existing systems is a true plus for MUOS. Immediate communication and the reception and distribution of critical data reinforces the capabilities of today’s warfighters to more productively counter the forces of destruction around the globe. The MUOS constellation is yet another advanced tool with which to apply effective force against those who wish us harm.